Agile Performance and
Autonomous Navigation
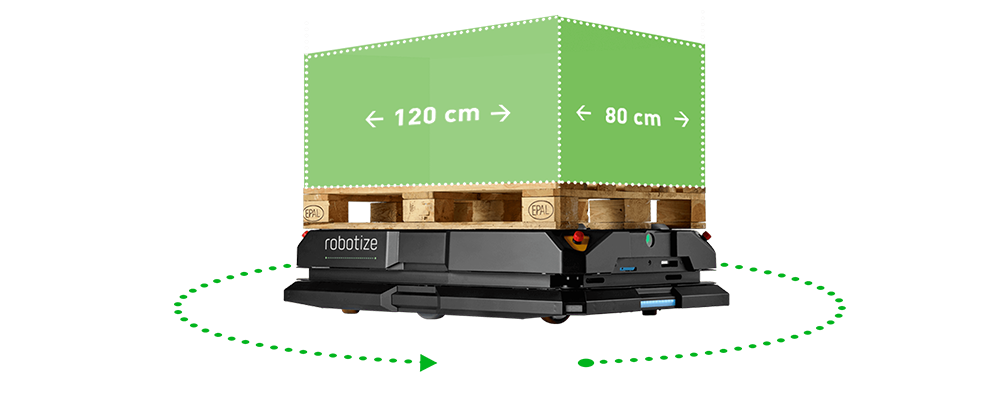
The GoPal AMRs only require the same space as an employee with a pallet jack. In addition, the robot can rotate about its own axis, making it much more compact and maneuverable than competing AMRs. These features are critical when work zones and traffic lanes at your site have been optimized for pallet jacks.
All GoPal AMRs feature smart navigation, allowing the robots to make dynamic decisions along their route. If the robot encounters an obstacle in its path (e.g., a person, fork lift or pallet jack), it will simply circumvent the obstacle. If the path is completely blocked, the robot automatically recalculates a new route and immediately proceeds to its destination.
Read our case studies to learn how the GoPal Solution have helped companies of all sizes automate their internal material transportation, while saving costs and elevating employees to more valuable tasks.
Using advanced light detection and ranging (LiDAR) technology, the GoPal AMRs can map and autonomously navigate dynamic working environments populated with people and static/dynamic objects.
Mapping the facility is performed in stages as follows:
- LEARNING STAGE: Simply take the AMR for a "stroll" (manually controlled using a smartphone/tablet) through your site to record the surroundings/environment using its sensors.
- ADJUSTING STAGE: Fine tune the resulting map (using GoControl) by, for instance, creating restricted areas and removing dynamic objects (which may have been recorded) from the map etc.
- LOADING STAGE: Once the map has been approved, load it into all the AMRs. The AMRs will now navigate autonomously on your site - safely mixing with employees, vehicles and other robots.